Search
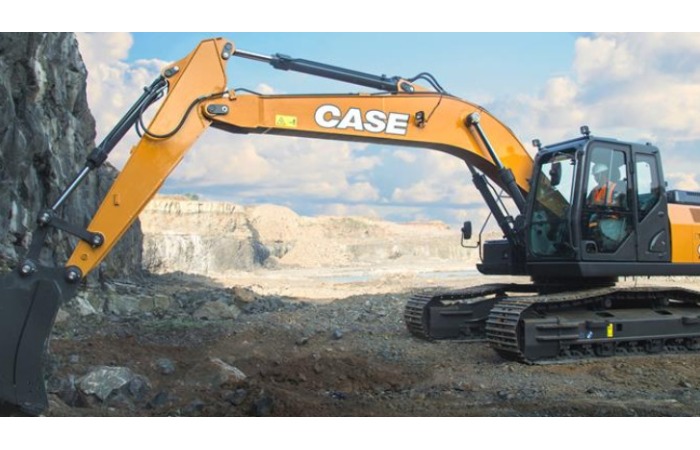
CASE Construction Equipment bags MP’s Best Employer Brand 2021
The construction equipment manufacturer has garnered this recognition for the second consecutive year.
CASE announces 60-day extension of warranty on all CE
CASE Construction Equipment announced a 60-day warranty extension on all construction equipment in light of the second wave of the COVID 19 pandemic in the country. This extension is applicable on all such units whose warranty is expiring between May 1, 2021 and June 30, 2021.
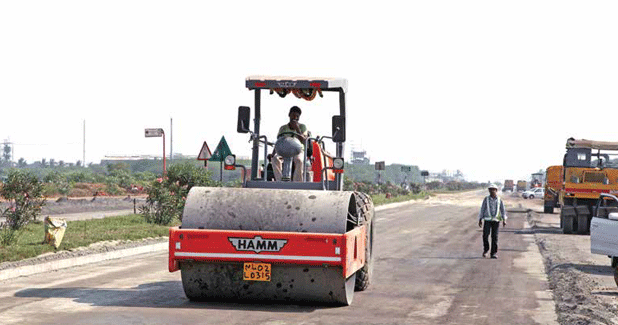
Intelligent Compaction
Performance and productivity remain key issues for compactor manufacturers, with firms keen to enhance output from their latest units. EQUIPMENT INDIA takes a peek into the features major OEMs have built in, in terms of improving machine

Maximising Output
Several key trends are emerging in the asphalt/soil compaction market where performance and productivity remain key issues. The OEMs are keen to maximise output from their latest units in terms of improving machine performance, O&M cost and operator safety and comfort.
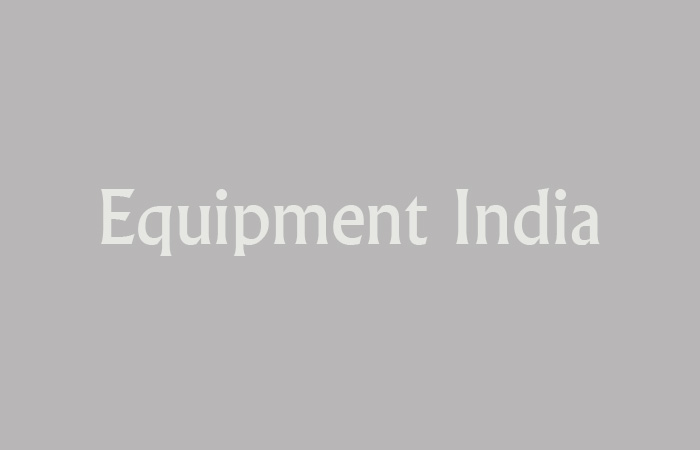
Compacting Technology Set to Improve
The new trend in technology is faster compaction by achieving the required density at a lower operating cost. Also, the latest equipment is designed with features to improve operator safety, comfort and maintainability.
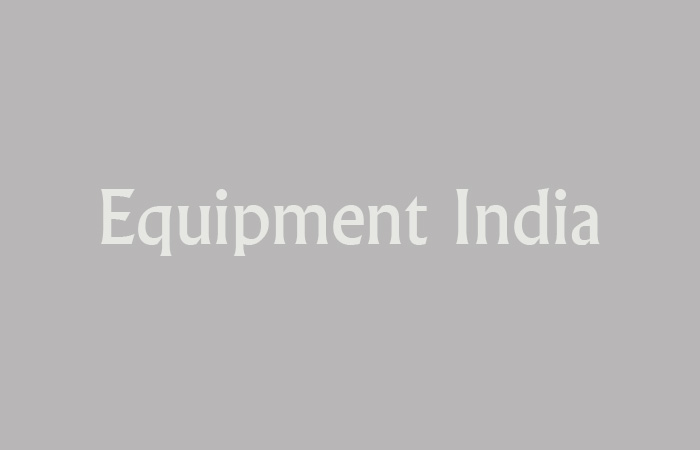
Caterpillar has vibratory soil compactors in the operating weight range of 4.5T?18.5T
The popular model being offered in India is the CS533E (11T Class) which is required to meet the National Highway Project requirements in India,? says Pankaj Dara, Associate Vice President - Construction, TIPL. 0 - - 15633 14 102 2011-05-02 00:00:00.000 Equipment India Hamm is the technology leader in compaction equipment
?Our existing manufacturing facility can produce 400 machines annually and plans are on for further expansion in the coming years,? says Girish Dixit, Head - Engineering & Design, Wirtgen India. In a freewheeling chat, Girish speaks about the industry trends.
Tell us about the range offered in compaction equipment and also their unique features?
Wirtgen India offers Hamm-11T soil compactor, 9T asphalt compactors and 24T pneumatic tyre rollers (PTR) for the Indian market. Hamm compactors come with German design and technology mainly featuring excellent operator comfort and safety. The equipment are powered by a fuel-efficient and highly durable water-cooled engine.
Hamm is the technology leader in compaction which has been awarded many design prizes for its latest innovations. Recently, it was awarded iF-Gold award 2010 also called the Design Oscar for new HD+ series of asphalt compactor. The GRW 280, rubber-wheeled rollers received the iF Design award 2010.
Higher quality level of the components used in Hamm compactors increases the durability of the equipment. Better serviceability and reduced maintenance frequency with less fuel consumption results in the lower operating cost of the equipment.
What is the existing manufacturing capacity for these product lines?
Our existing manufacturing facility can produce 400 machines annually and plans are on for further expansion in the coming years.
What is the rental scenario for these products?
Currently, Wirtgen India is not in the rental market and is only selling the new equipment in the retail and corporate segments, rental companies.
Are these products compliant with the Bharat stage III emission norms?
Yes, the equipment built after April 2011 will comply with Bharat stage III emission norms.
How do you look at the replacement/ repowering market for the units sold which are not complying with Bharat stage III norms?
As per the regulations, no replacement/re-powering is required for the units built with Bharat stage II norms.
Why vibratory compactors over static ones and what is the vibration effect in compaction over the static loading?
Vibratory compactors develop dynamic force in addition to the static load and total applied force is the sum of dynamic force and the static weight of the machine. For example, Hamm 11T soil compactor generates 24T dynamic force and with 6.8T static weight at the drum will induce 30.8 tonne load on the ground. The advantage of using 11T vibratory soil compactor versus 30 tonne static compactor is evident from this.
The vibratory compactor with drum vibrating at higher amplitude will result in compacting the higher lift thickness and achieving the required density compared with the static roller. In the static roller, the linear load is not uniform over the width of the machine (one front roller and two rear rollers) which results in uneven mat finish. In the vibratory compactors, the linear load is uniform along the width of the drum.
To what extent do soil conditions determine the selection of compactors? Could you tell us the reasons?
Type of soil and conditions like moisture content decides the achievable density within the required number of passes. It is important to select the suitable compactor which will develop the required force to achieve the density with lesser number of passes on the appropriate lift thickness.
What determines the maximum achievable density?
Density depends on the soil characteristics (type of soil) and optimum moisture content (OMC) present in the soil. Generally, 95 to 100 per cent density can be achieved with 11T soil compactors on the appropriate lift thickness.
?To have maximum return on investment, the equipment should have maximum productivity and less rework,? says SM Roy, Chief Executive Officer, Lanco Infratech. In an exclusive chat with Equipment India, Roy elaborates on the evolution of compacting and grading technologies. Excerpts from the interview.
How, over a period, have the methods of compaction and grading evolved and to what extent does the contracting fraternity use the advanced equipment and methodology?
The first road roller was horse-drawn; this was followed by steam and diesel rollers. For a long period, static compactors of various sizes were used. The introduction of vibratory compactor in 1946 opened a new era in construction industry.
A few decades ago, grading was done manually or with tractor dozers where operator skill was important for accuracy. Advanced technology has made the grading work simple by giving option of automatic slope and elevation offsets. GPS navigation and machine guidance systems have reduced the amount of external surveying required.
Almost every construction project or site preparation requires some kind of grading and compaction. The Indian contracting community extensively uses the graders and compactors for various purposes based on size and extent of projects.
Why vibratory compactors over static ones? What is the vibration effect in compaction over static loading?
Static compactor functions with its own weight and hence compaction is confined to the top soil layer. Vibratory compactors use a mechanism to create a downward force in addition to the machine's static weight thereby affecting the top layers as well as deeper layers. Vibration moves through the material, setting particles in motion and moving them closer together for the highest possible density.
To what extent does the soil condition determine the selection of compactors?
The desired level of compaction is best achieved by matching the soil type with its proper compaction method. Clay is cohesive; its particles stick together requiring high impact force to compact. Hence, the sheep-foot roller is the best choice. Best compaction of granular soils is possible with shaking or vibratory action. For mixed type of soils, it is a good idea to choose the compactor appropriate for a larger percentage of the mixture.
What is the return on investment on a compactor and on a grader?
To have maximum return on investment, equipment should have maximum productivity and less rework. Production cost depends on depreciation, maintenance, fuel, working hours and labour. Smaller machines cost less in terms of ownership but more in labour and vice versa. In general, for each situation, one should study equipment productivity and try to strike a balance to get better value for money.
Could you tell us about the density achievable from the range of compactors? What determines the maximum achievable density?
The maximum achievable density depends on fill type, compactive efforts and moisture content and it varies from 2.1 tonne/cu m for well graded gravels to 1.5 tonne/cu m for highly plastic clays. Most of the compactors can achieve maximum fill density with different compactive efforts and efficiencies.
What are the variants in compaction?
The variants in compaction are soil type, moisture content, lift or fill thickness, compactive efforts or number of passes of compactors.
Selection Criteria:
A selection criterion for graders and compactors is given below:
? Size, weight and machine power.
? Steering, direction control and maneuverability.
? Functional automation.
? Multi-tasking machine with various attachments.
? Maximum possible thickness of the lift (for grader).
? Accuracy of the grading (for grader).
? Range of vibration frequency (for compactor).
? Working and downtime.
? Ownership and maintenance cost.
? Availability of trained manpower to use the machine.
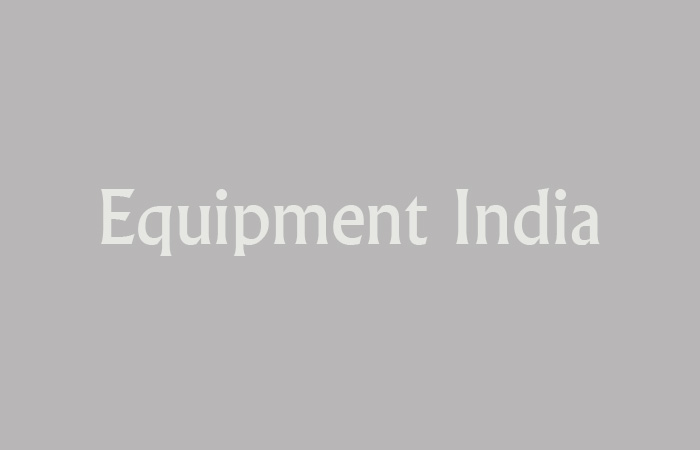
Vibratory Compactor Vs static
Agith G Antony finds out the technical aspects of compaction from Pradeep Kathuria, Head -Essar Equipment Bank, Essar Projects India.
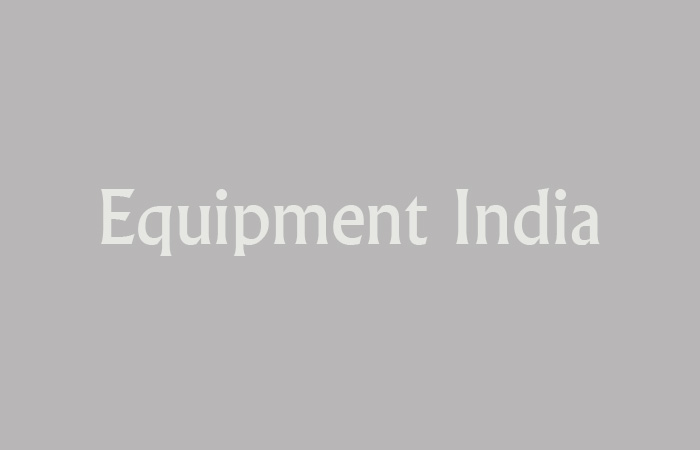
The Road Ahead
With more than 60 per cent of the cargo movement done by India's large network of roads, the road-building sector in the country has offered major growth opportunities for the construction equipment industry.